Did you know that depending on your application, you may want to add a special lining to the inside of your pump? Most municipal applications that pump wastewater do not need a special lining. However, lining your pump can play an important role in wear resistance and the reduction of pump downtime if you’re pumping:
- Low viscosity sludges with high run times
- Lower viscosity sludges with abrasives sludges or high grit content
- Septage, which can have a high sand content
- Water treatment residual sludge, lime slurry and lime sludge
- Fats, oils and grease that can coat the internals
- Chemicals and highly abrasive materials
Choosing the Right Coating for Your Application
There are a variety of different coatings that can be used inside of your Double Disc Pump should your application require it, including porcelain enamel, powder coating, PVC or neoprene. Each protects the inside of the pump from wear differently, depending on what it is you are pumping.
Porcelain Glass Enamel
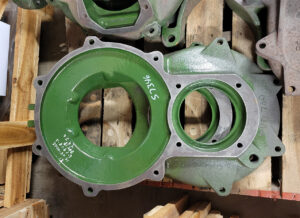
Porcelain glass enamel, also known as glass lining, glass-lined steel or glass fused to steel, is a coating that can be applied to sheet steel, cast iron or aluminum in storage tanks, piping and pumps. The enamel, which is used for industrial purposes, helps to improve chemical resistance and abrasion resistance. The most important characteristic for use in industrial applications is its ability to protect against corrosion. Porcelain enamel can withstand high temperatures and thermal shock.
PVP suggests using this type of lining for applications that pump lime slurry, lime sludge, water treatment plant sludge, septage and grease applications.
Powder Coating
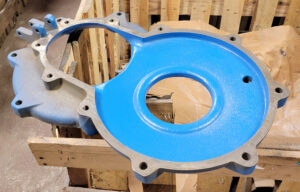
Powder coating is a high-quality finish that protects machinery that performs some of the most extreme jobs. It provides a more durable finish than liquid paint. Items that are powder coated are more resistant to moisture, chemicals and abrasives. Powder coat, which is a polymer resin system that is combined with curatives, pigments, leveling agents, flow modifiers and other additives, is applied as a free-flowing, dry powder electrostatically and then cured under heat or with ultraviolet light.
PVP uses powder coating for its pumps that will come in contact with lower viscosity sludge, as well as some return activated and waste activated sludge applications, because it can withstand scratches, chipping, abrasions, corrosion, fading as well as wear issues.
Neoprene or PVC
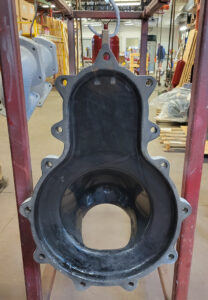
For applications with the toughest abrasives and aggressive chemicals and caustic materials, PVP uses either neoprene or polyvinyl chloride (PVC) inside of its pumps.
Neoprene is a synthetic rubber compound that is chemical resistant and can protect against a wide range of oils, acids, caustics and solvents. This synthetic rubber is also resistant to water and heat.
PVC offers a high degree of inertness and resistance to corrosion. It is free from bio-film contamination that can be a breeding ground for bacteria. It can be applied seamlessly in various thicknesses depending on requirements. PVC also prevents unnecessary water waste from source to consumer.
Our Engineers Help You Choose
Penn Valley Pump application engineers will choose a lining, if required based on your application. We will choose the pump lining that will work best for your application to ensure your pump will operate for years without failure.